Technical Talk with David Biggs
Words: David BiggsBonding with Masonry
By David Biggs
I hope you had a good summer! Masonry construction has been very active and brought about some new questions.
We are in the midst of another winter building season and the questions keep coming in! Here are a few more.
Q: A contractor writes that the specifications for a recent project required that the Concrete Masonry Units must meet ASTM C90, Type I, Grade N. They were confused and wanted to know how to satisfy this criterion?
A: The short answer is that you are only required to meet ASTM C90. The reason is the type and grade for the units that are listed in the project specifications were removed from the ASTM standards in 2000. The type used to designate moisture-control; the grade used to designate strength and moisture penetration resistance, either N or S. Despite designations were dropped 18 years ago, it is surprising how many times this exact issue shows up in project specifications and drawing notes.
The problem here is that many designers recycle old specifications and have not updated their masonry specifications. The solution is that architects and engineers can get assistance from the masonry industry. Most technical representatives of manufacturers of CMU, brick, stone, etc. as well as masonry institutes will review architect and engineer specifications and provide updated information. Other sources of specifications are the AIA Masterspec and The Masonry Society’s TMS 602, Specifications for Masonry Structures. Since TMS 602, as well as TMS 402, are referenced documents in the building code, designers should already have this document.
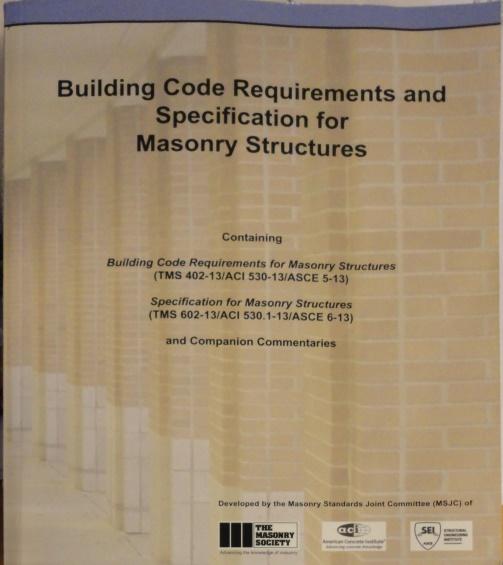
Figure 1- TMS 402 and 602 referenced by the building code
Q: Interestingly, we have two similar questions, but from two different vantage points.
Question 1 comes from an engineer: On our designs, we always specify 3,000 psi concrete for bond beams. The contractor said it should never be concrete and it should be masonry grout. Is that correct? Isn’t concrete the same as masonry grout?
Question 2 comes from a contractor: The engineer on a project rejected our submittal for concrete fill to be used on bond beams. They insisted we use masonry grout per the specifications. In our area, concrete is less expensive than masonry grout and aren’t they the same anyway?
A: While it does seem logical to that concrete with being used with masonry, particularly concrete masonry, the answer to both questions is that only masonry grout should be used, not concrete. This is actually a building code issue since TMS 402 and TMS are referenced standards in the code and they require masonry grout meeting ASTM C476, not concrete. Now, for the reasoning.
- What is similar about masonry grout and concrete?
They have similar constituent materials. In general, masonry grout has Portland cement, lime, water, and fine aggregates. Masonry grout is distinguished as either “fine or “coarse” based upon the size and quantity of the aggregates in conformance with ASTM 404, Standard Specification for Aggregates for Masonry Grout. In accordance with ASTM C476, Standard Specification for Grout for Masonry, “fine grout” aggregates are sand and range from 75-μm (0.002 inches) to 9.5 mm (3/8 inches) with the majority being approximately 1.18 mm (3/64 inches). “Coarse grout” aggregates are a blend of sand and stone that range from 600-μm (0.023 inches) to 12.5 mm (1/2 inches) with the majority being approximately 9.5 mm (3/8-inches).
Basic concrete has Portland cement, water, and aggregates. Concrete aggregates include a blend of sand and stone in conformance with ASTM C33, Standard Specification for Concrete Aggregates. Comparing the information in ACI E1-16, the sand gradation is almost identical to the masonry grout “fine aggregates”. But, the stone ranges generally up to 1-inch size with the majority being approximately ½ inch.
- What is different about concrete and masonry grout besides the aggregates?
Water content is a major difference. Masonry grouts requirement a higher slump (8”-11”) per ASTM C476. This provides adequate moisture to absorb into the masonry units and provide a grouted bond. Concrete slump are traditionally in the 4” to 6” range. When concrete is used with masonry units, the moisture in the concrete could be absorbed into the units and cause shrinkage that leads to inadequate bond. In Figure 1, the bond beam is filled with stiff concrete rather than masonry grout. The concrete does not flow and improperly bridges the cells below.
Figure 1 also shows another distinct difference between masonry and concrete in the construction. Notice the space between the reinforcement and the face shells of the bond beam. Using masonry grout, those spaces can be ¼ inch when using fine grout and ½ inch when using coarse grout. The small aggregate and the high slump allow the grout material to flow around the bars. For masonry, space plus the face shell thickness together form the cover for reinforcement in masonry construction for corrosion protection and fire protection.
With concrete construction, the cover over the bars is purely concrete. The concrete cover accommodates the larger aggregate in the concrete.
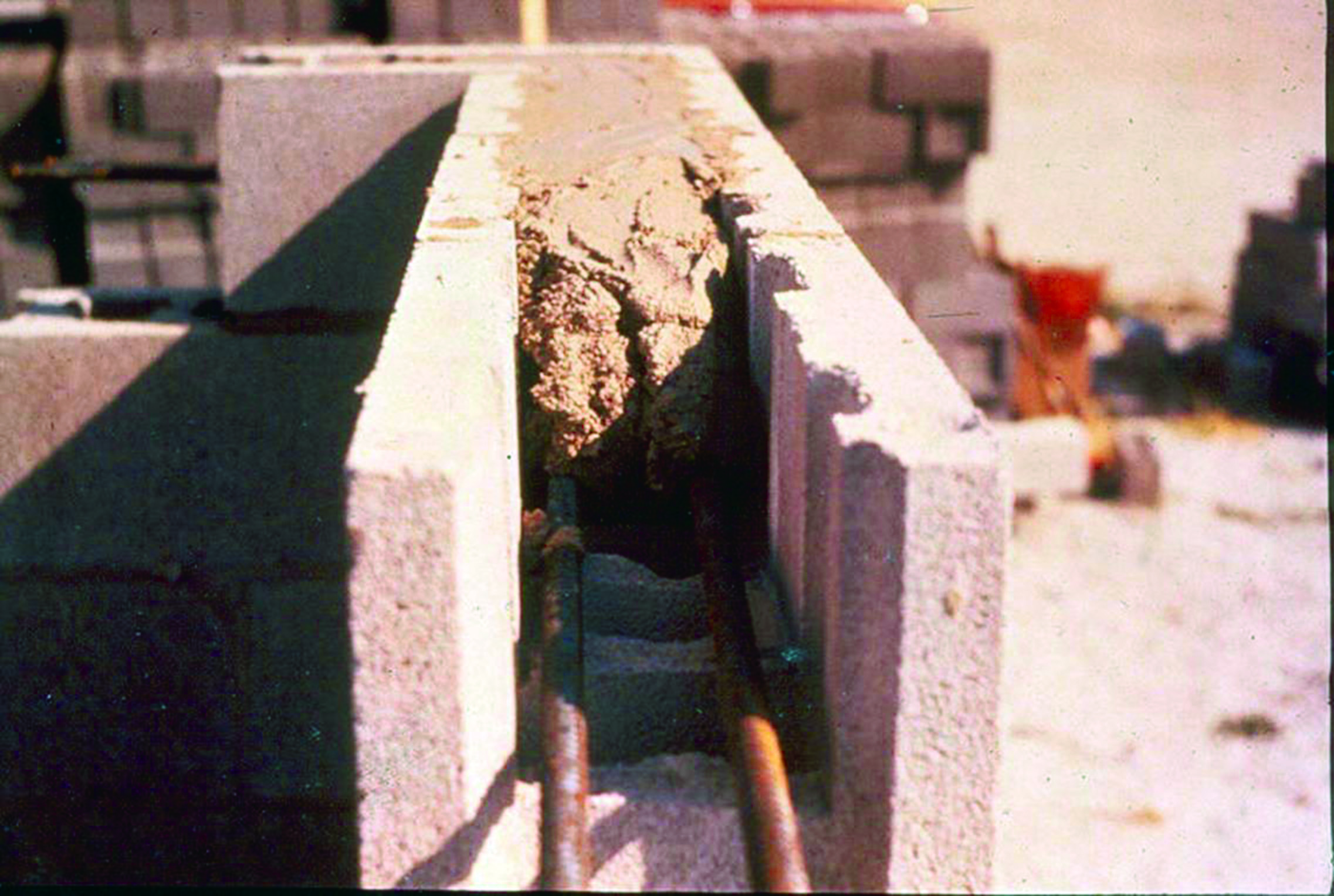
Figure 2- Bond beam wrongly filled with concrete
So, there is a distinct difference between concrete and masonry grout. Concrete with large aggregate and low slump will not flow around the masonry reinforcement. Designers need to update their specifications to remove the use of concrete in bond beams and any reinforced cells. Mason contractors need to recognize that concrete is not equal to grout and they should use the correct grout material.
Q.This question comes from a mason contractor. On a recent project, the engineer cited our work for non-conformance because the lap splices were not wire tied. The engineer and masonry inspector indicated “Per the General Notes for Masonry on construction document, the concrete block construction is to comply with “Building Code Requirements for Masonry Structures” TMS 402 / ACI 530 ASCE 5. This Code requires that splices of reinforcement be lapped, welded or mechanically connected.” Further, they state…” vertical reinforcement has been lapped by installing rebar adjacent to rebar once the grout has been poured into the open CMU cells. The vertical rebar at the laps has not been tied together.” Finally, “The structural engineer recommends compliance with CRSI with regards to reinforcement lap splicing. CRSI indicates that the reinforcement is in contact and fastened together (a contact lap splice) to prevent displacement beyond the tolerances allowed by construction loads or by the placement of grout or mortar.”
We’ve always been told that reinforcement does not have to be wired tied. Has something in the code changed? This requirement was not stated in the project specifications.
A. Your question raises issues beyond the issue you mention regarding wire tying bars. Let’s go through the issues starting with wire typing bars.
1.Wire Tying Reinforcement: The engineer and inspector’s notification indicates the lap splices in the CMU are to be tied and cites CRSI as the justification. It also implies that all laps must be contact splices. The notification justifies these through the use of a drawing note “…the concrete block construction is to comply with “Building Code Requirements for Masonry Structures” TMS 402/ACI 530/ASCE 5.” There are several issues here:
a.“Building Code Requirements for Masonry Structures, TMS 402/ACI 530/ASCE 5” applies to the design. Construction is governed by “Specification for Masonry Structures, TMS 602/ACI 530.1/ASCE 6” as stated in the building code as shown below.
“SECTION BC 2104, CONSTRUCTION
2104.1 Masonry construction.
Masonry construction shall comply with the requirements of Sections 2104.1.1 through 2104.5 and with TMS 602/ACI 530.1/ASCE 6.”
As mason contractors, you are not responsible to meet TMS 402/ACI 530/ASCE 5. Therefore, the project note should have referred to “Specification for Masonry Structures, TMS 602/ACI 530.1/ASCE 6”.
In TMS 602/ACI 530.1/ASCE 6, masonry lap splices are not required to be tied. The standard states:
“3.4 B. Reinforcement
- Support reinforcement to prevent displacement caused by construction loads or by the placement of grout or mortar, beyond the allowable tolerances.”
Thus as the contractor, you must support the bars from displacing during grout placement. While tying the bars is one option to accomplish this, it is not mandatory. A more commonly used option is to utilize one of the many positioners available on the market. So, the answer to your question is no, there have been no changes that mandate tying bar splices.
- The citation mentions the requirement for compliance with CRSI. The CRSI document is a very well written technical note. However, it applies to reinforced concrete and ACI 318, not masonry. The word “masonry” never occurs in the note.
In addition, the CRSI is not in the project specifications for masonry and it is not a referenced standard in TMS 602. Thus as you stated, wire tying was not in the project specifications; imposing that requirement during construction would amount to a contract change.
- Contact lap splices: Implied by the requirement to wire tie lap splices is that bars must be in contact. TMS 602 actually allows non-contact lap splices which physically can’t be tied. Article 3.4B.9 from the masonry specification states:
“Noncontact lap splices — Position bars spliced by noncontact lap splice no farther apart transversely than one-fifth the specified length of lap nor more than 8 in. (203 mm)”.
This further reinforces that bar splices need not be wire tied.
- Grouting: One concerning the item in the citation that was “..vertical reinforcement has been lapped by installing rebar adjacent to rebar once the grout has been poured into the open CMU cells”. If there was a reason for citing you for non-conformance, this was it. TMS 602, Article 3.2E states:
“3.2 E. Reinforcement — Place reinforcement and ties in grout spaces prior to grouting.”
This article requires the bars to be positioned prior to grouting, not after. Your method of “wet sticking” may be part of your company’s standard low-lift grouting method, but it is not in conformance with masonry standards. Therefore, it should be presented and accepted by the project engineer and inspector prior to starting work. If you did not get that acceptance, the work is in non-conformance.
That’s it for this month. Thank you again for following this column. Remember, by bonding, we get stronger! Send your questions to info@masonrymagazine.com, attention Technical Talk.
David is a PE and SE with Biggs Consulting Engineering, Saratoga Springs, NY, USA. He specializes in masonry design, historic preservation, forensic evaluations, and masonry product development.