The concrete is required to have an average compressive strength of the five specimens tested of at least 2,100 psi, with no individual specimen testing lower than 1,800 psi.
Freeze-Thaw Durability
Durability testing is also required because resistance to freeze-thaw effects cannot be reliably predicted based on factors such as compressive strength, absorption, or concrete density. As for compressive strength, testing takes place on concrete samples, rather than on the MSV units themselves. From the MSV concrete mix, five cast concrete beams are prepared and cured, then tested according to ASTM C666, Standard Test Method for Resistance of Concrete to Rapid Freezing and Thawing, with some modifications. (See Figure 2).
Figure 2 – Freeze-Thaw Testing of Beams of MSV Mix
Shear Bond
Shear bond determines whether or not the MSV units can sufficiently bond with the mortar setting bed. Units are tested using a slightly modified ASTM C482, Standard Test Method for Bond Strength of Ceramic Tile to Portland Cement Paste, and must develop a shear bond of at least 50 psi.
The value of 50 psi is generally considered to account for differential shear stress between the adhered veneer and the backup system. The test method is used as a quality assurance test, as well as to verify the shear strength of MSV systems that do not comply with the construction requirements of ASTM C1780, Installation Methods for Adhered Manufactured Stone Masonry Veneer Units. (See Figure 3). For testing, the MSV units are cut into a test sample between 2-1/4 inches square and 4 inches square. The back of the sample must remain as manufactured, so that the test properly indicates the bond strength of the manufactured units.
Figure 3 – Shear Bond Testing of MSV Units
Density and Dimensions
ASTM C1670 includes requirements for thickness and face size of the MSV units, as well as a maximum weight per square foot of wall to facilitate handling and installation, as well as to help ensure good bond between the unit and the setting mortar—overly large or dense units will be more difficult to handle and place, and may tend to pull away from or slide down the mortar setting bed.
Determining the thickness, area, and volume (hence density) of MSV units is not necessarily straightforward, because the units are
intentionally of varying thickness and are often not rectangular. For this reason, ASTM C1670 includes a requirement for an absorption test to be performed and results reported, even though there is no absolute absorption requirement for the units. The absorption testing provides saturated and immersed weights of the units sampled for testing, which are used to determine the saturated density and the unit volume. These values, in turn, are used to determine the average thickness as well as the weight per square foot of the units.
MSV units are required to have a minimum thickness of 1/4 inch, although there may be thinner spots in the area within 1/2 inch of the unit edge. The average unit thickness must be no reater t an 2-5/8 inches, and units cannot exceed 36 inches in any face dimension, nor more than 5 sqft2 in total face area. Finally, the weight of the units cannot exceed 15 lb/sqft2. These requirements for size and weight are consistent with current building code requirements for adhered veneer masonry units.
Linear Drying Shrinkage
Like other concrete materials, the concrete used to produce MSV units must meet a maximum linear drying shrinkage criteria—often simply referred
to as ‘shrinkage.’ When wetted, most materials increase in size (swell) due to the absorption of water. As these materials dry out, their volume decreases back to the pre-wetted state. This phenomenon applies to concrete materials as well, although the total amount of shrinkage is very small.
The drying shrinkage test essentially brings a molded specimen of the MSV concrete mix to equilibrium in moist storage, then brings the
same specimen to equilibrium in air storage, and measures the shrinkage of the specimen during this drying process. As an example, if during testing the specimen shrinks 0.001 inches over an 11-1/4-inch length, then the shrinkage for this unit is (0.001/11.25)*100 = 0.008%...which is less than the 0.10% maximum shrinkage required by ASTM C1670.
Finish and Appearance
Finish and appearance provisions limit defects that would detract from either the appearance
or performance of the MSV installation, but permit minor chips and cracks incidental to usual manufacturing and handling methods. These requirements apply at the time the units are delivered to the jobsite. At delivery, the finished faces of the delivered units should be compared to an approved sample that includes the range of unit textures, sizes, and colors selected. The approved sample can be manufacturer’s samples, individual units, or field mock-ups when specified.
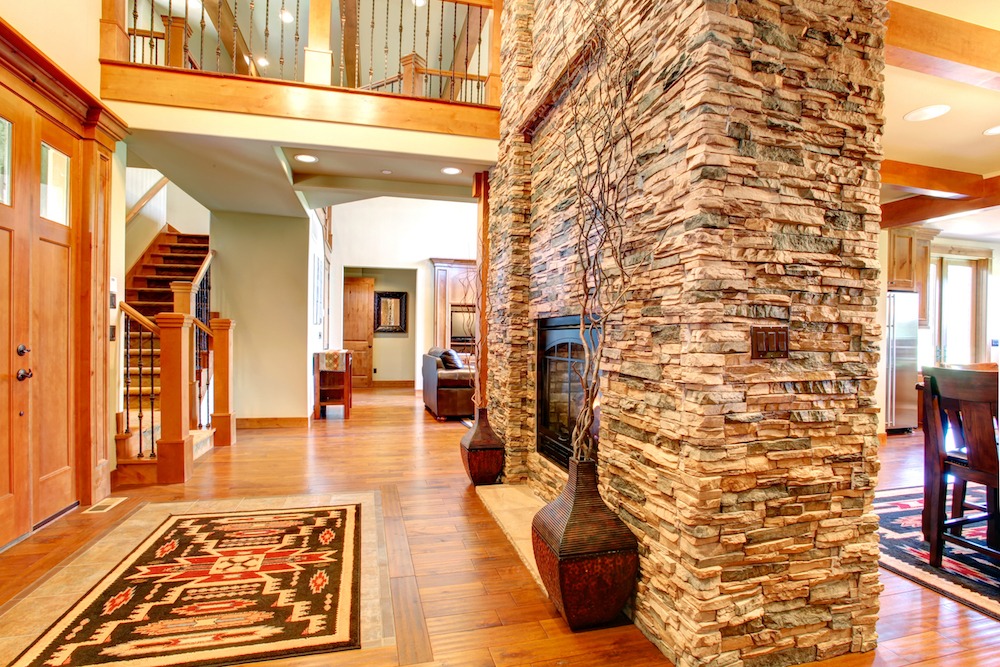
Up to 5% of a shipment is permitted to contain: - broken units,
- units with defects or protrusions that interfere with installation or otherwise impair the MSV performance,
- chips larger than 3⁄4 inch in the finished face, or an aggregate length of chips exceeding 10% of the unit perimeter,
- cracks, crazing, scuffing, or other imperfections in the finished face that detract from the appearance when viewed from a distance of 20 feet under diffused lighting.
Although C1670 limits the number of broken units, keep in mind that broken units are often usable during installation, and in fact MSV units are commonly broken or saw-cut by the installer to fit into particular areas of the construction for field stone and other random stone patterns.
Summary
Even though it is a popular cladding material, adhered manufactured stone masonry veneer has historically not had a national, consensus-based specification to set minimum properties for these products, which in turn has sometimes been a source of performance issues in the field.
The publication of ASTM C1670 and its inclusion in the 2018 IBC, however, effectively raises the bar for the quality and consistency of MSV units, providing a comprehensive set of physical criteria to help ensure successful field performance. Compliance with C1670 provides more consistency within the industry, as well as higher confidence in the product from designers and building code officials.
Words: Nick Lang and Maribeth Bradfield
Photos: NCMA, Masonry Magazine
Sidebar:
What is Adhered Manufactured Stone Masonry Veneer?
Adhered manufactured stone masonry veneer (AMSMV or MSV) is a manufactured concrete product increasingly used to economically provide the look of natural stone to buildings large and small. MSV is known by a variety of names throughout the country, including precast stone veneer, architectural precast veneer, cast stone veneer, simulated stone, as well as a by several of the popular brand names under which it is sold.
MSV installations are similar in color and texture to natural stone and are used as a non-load bearing exterior veneer or as an interior nish and trim on concrete, masonry, wood stud and light gage steel stud walls, as well as on metal buildings. Manufactured stone veneer products are available in a wide array of colors, textures and patterns, providing an almost limitless palette. As a veneer product, MSV’s primary function is to provide a beautiful, durable nish to a wall system. Product lines include not only a large variety of styles and colors, but also specialty units to make installation easier, such as corner units, sills, hearthstones, and caps.
MSV provides all of the advantages of other masonry materials, at a lower price and wider availability than natural stone. Because of the lighter weight and manufactured at back, MSV units are also easier and quicker to install than natural stone.