Outdoor Living: From The Eyes Of A Contractor
Words: Dean Marsico
Words and Photos: Dean Marsico
It is not an easy task keeping up with all of the changes in the construction world. The time we spend keeping ourselves and our companies informed and up to date with these changes can take a lot of hours out of our days, weeks, months, and years. A large adjustment for us that has hit all phases of our business, whether you build large commercial projects, residential developments, or single family homes is outdoor living.
Outdoor living is a must. Rooftop living spaces in urban areas, outdoor rooms in suburban developments, and lifestyle spaces in large office complexes have become the norm. Architects and designers are spending a great deal of time and energy designing these areas because the marketplace demands it, and quite honestly has become somewhat obsessed with bringing the indoors atmosphere outside.
Today there is an expectation in our business that you should know everything. No pressure right? Changes in products, building structures, and codes can be overwhelming. I have been very lucky in this business because I get to see it from both sides. I have spent many years designing and installing all kinds of projects in the Boston area and around the country. I traveled for seven years working on two television shows. One show focused on masonry and the other focused on outdoor design.
Today I have a completely different perspective. I, along with my cousin, help run one of the largest working quarries and supply operations in Southern Massachusetts. Trying to keep up with all the new products and installation techniques is a huge part of the daily operations here at Plymouth Quarries. It is our job to make sure we keep our contractors up to date with everything the world of hardscape and outdoor living has to offer.
The stone and hardscape segment of the market is exploding with both new product development and demand. Each week I get a call from manufacturers offering new stones from all over the world. The leading concrete paver manufactures are also constantly introducing new colors, textures, and sizes of their products. The competition is fierce and they want to stay ahead in product development and the changes in design and technology.
This year for example, very early on in the season, I have seen a dramatic change in how we prepare and install our projects. We offer many classes at our facility for our masons, landscapers, and designers. The most recent change has come from concrete paving manufactures. All of the top companies have replaced the base preparation for all of their products, which is pretty significant from the old way of doing things. Up until this year’s installation for walkways, patios, or driveways consisted of three to four inches of compacted base material known as crusher run or dense pack. The names of this material can change depending on what part of the country you live in, but the material is basically the same.
Crusher run is a stone material consisting of fines and crushed stone usually three-quarters of an inch that when compacted lock together to give a solid base for any installation of asphalt, pavers, and stone. The top setting base consisted of a one-inch layer of course sand. This year it has been thrown out the window. The representatives from the paving manufacturers are now instructing all installers to prepare a base comprised of three-quarter inch crushed stone with a setting bed of quarter-inch flake stone.
Flake stone is a finer stone that almost looks like corn flakes cereal. For architects, contractors, and designers, keeping up with these installations specifications is a must because the manufactures will not warranty their products if they are not installed by their specifications. The change in the installation hasn’t really been too surprising for us here on the East Coast.
Permeability is steadily becoming a requirement for many of our seaside communities from Boston to Cape Cod and the Islands. These local towns insist that every driveway, walkway, or patio must be permeable whether it is located on the shoreline or inland. If you haven’t gotten up to speed on permeability I strongly suggest you start. In the next few years, I believe it will affect every paving, hardscape and outdoor living installation around the entire country.
Permeable when constructed properly will help prevent major water runoff in heavy storms, which in turn will help alleviate undue stress on the sewer systems. The goal is to allow the water to naturally filter through the environment. While I’m on the subject, let me try to clarify what makes a permeable paver permeable. The paver itself isn’t permeable. It is the joints in between them that allow the water to flow through.
Pavers that are labeled “Permeable” are manufactured with spacer’s that uniformly space the joints as they are laid. You can make any stone, brick, or concrete paver permeable as long as the joints have the correct spacing and the base is prepared correctly with the right size crushed stone layers. I strongly encourage contractors, designers, architects, and homeowners to reach out to their local suppliers to find out what is required in your area by the local building codes.
Here at Plymouth Quarries, we encourage installers to use a permeable base for any kind of stone patio or walkway. Our reasoning for this is because over the years some serious issues have come up with the sedimentary stone products. We have heard of issues like severe flaking of the top layer occurring over very short periods of time. One story, in particular, occurred on a large pool area that after only being installed for less than a year completely flaked. Luckily for us, it wasn’t a job we supplied. There can be any number of reasons this pool area degraded so quickly. One of the most common factors starts with the installation.
If I had to guess the contractor set the stone in a base consisting of compacted stone dust. Stone dust packs great, but it doesn’t drain and holds water. When you add polymeric sand to the joints the stone is surrounded by water underneath and on the sides. When water doesn’t have a place to go, and it is in an environment that gets severe winters with freeze-thaw cycles, the outcome will not be a desirable one. We want to make sure water never sits on the top, the sides, or the base of any product used outside in paving, or veneer.
As contractors, we are always concerned about water management and want to minimize any potential issues. Making your projects permeable will help take away that risk and avoid major problems down the road. The actual cost for labor and materials shouldn’t change. There will be a cost increase depending on what product you choose for the jointing material. The lower cost choice would be filling the joints with chip stone that is swept in. Over time you might have to do some refilling and some might wash onto the patio after heavy rains. The more expensive choice is epoxy sands. These epoxy sands are squeegeed into the joints and after they cure get very hard, but allow the water to flow through.
Product choices are numerous. We live in a big wide world today where we can get products shipped to us from any corner of the globe. Our customers have information at their fingertips constantly using search engines like Pinterest or Houzz where they can spend hours looking at all types of products and all types of designs. I always have an eye out for new products that will hopefully be the next big thing for our contractors and homeowners.
Finding new products is the easy part, making sure they are the right choices for our weather conditions is a must. Softer stones used outside in the Boston area will never survive our climate and are a waste of money. Manufactured products can also have issues. Things like low psi, top layer color mix only on the surface will make them fade in a very short time. Make sure you know your products. I have written many articles about Thin Veneer stone, so I don’t want to be repetitive.
Let me just say this, if you are not familiar with thin veneer stone and brick by now, you are left behind. The types of thin veneers available today are endless. You can find any kind of color or cut. They are great choices for outdoor fireplaces, fire pits, bars, and built-in kitchens, and offer huge savings on cost and labor. Every supply store across the country supply these products and the learning curve for design and installation is not very difficult.
After you take time researching and choosing the hardscape products for your outdoor living spaces I encourage you to take a breath and look up. I have learned this lesson over many years and looking up allows me to see the whole picture, not just the hardscape or masonry material. The goal is to make any design incorporate all of the elements to make it a true outdoor living space. Let’s start with furniture. The choices in quality, design, and cost cover the spectrum.
Beautiful couches with large comfortable cushions in all different colors and styles made for the outdoors but look like a great choice for the inside of your home. Dining tables, made with high-end woods, metals, and composite materials. I have used many of these in my designs and I believe they are just as important as choosing big-ticket items like the stone and paving products.
Today outdoor led lighting is a must. The cost has dropped dramatically and the quality of the lights themselves is top notch. Outdoor lighting done right can make an average design look high end. Lighting goes hand in hand with another must-have, which is plantings. These are ignored in many designs. Decorative garden pathways softly lit with greenery, and a centerpiece tree that has a beautiful canopy, which, is illuminated at night, is an incredible addition to any outdoor living design.
Even when space isn’t being used you will find yourself staring out of the window looking at the space because all of the lights create such a stunning atmosphere. I tell designers and homeowners all of the time if the budget is becoming an issue, cut down on the size of the patio and put your money into lighting and plantings. As a mason, I can build you the most amazing high-end stone patio but if you don’t add the finishing touches it ends up being just a patio.
Our customers, both commercial and residential demand more out of our designs. We aren’t just building patios we are building outdoor rooms. We truly are a resource center. We educate about installation, we give design options, and we introduce our clients to all of the new and exciting products that are available. Changes in taste and design styles are constant. Recently the word “Eclectic” keeps coming up in conversations with many of my customers.
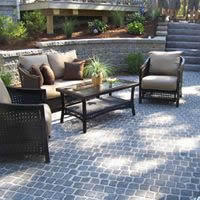
I live and work in an area that is surrounded by history. Many of these historic towns have old farmhouses built with stone foundations surrounded by 200-year-old farm walls used as property boundaries. They are not really the most desirable backdrops for eclectic or modern design. The challenge in designing for these homes is merging the old world into the new world. It can be a difficult task especially when someone owns a home built in the 1800s and has a taste for very a modern clean design. Luckily I have many product options at my fingertips that allow me to satisfy my customers and stay true to the design of the home and neighborhood they live in.
This is such an exciting time in our world of outdoor living. The business and market place have changed so rapidly which has brought incredible opportunity for us to grow our business and increase our profit margins. Every one of our customers wants some kind of outdoor living space, and we are very happy to help them make their dreams come true.